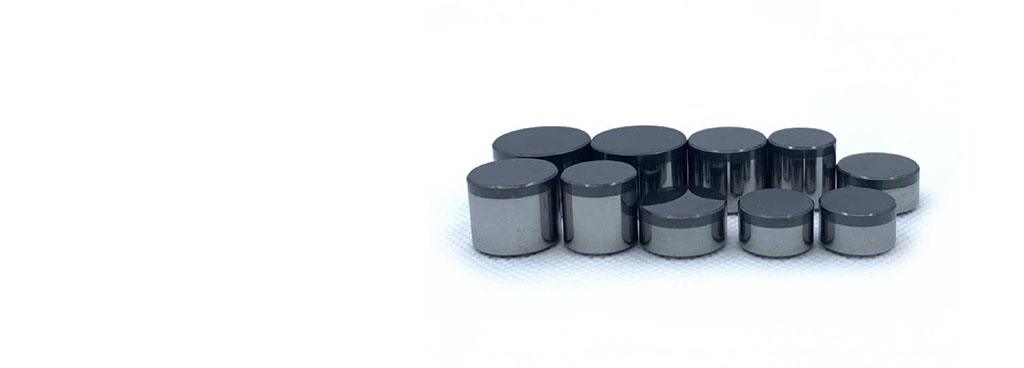
# Best PDC Cutter for Superior Drilling Performance
## Introduction to PDC Cutters
Polycrystalline Diamond Compact (PDC) cutters have revolutionized the drilling industry with their exceptional durability and cutting efficiency. These advanced cutting tools are widely used in oil and gas exploration, mining, and geothermal drilling applications. The right PDC cutter can significantly improve drilling performance, reduce downtime, and lower overall operational costs.
## What Makes a PDC Cutter the Best?
When selecting the best PDC cutter for your drilling operations, several critical factors come into play:
– Diamond table thickness and quality
– Tungsten carbide substrate composition
– Interface design between diamond and substrate
– Thermal stability and wear resistance
– Cutting edge geometry and chamfer design
## Top Features of High-Performance PDC Cutters
### 1. Superior Diamond Quality
The best PDC cutters feature high-quality synthetic diamond tables with uniform grain structure. This ensures consistent performance and extended cutter life even in the most challenging formations.
### 2. Advanced Bonding Technology
Premium PDC cutters utilize innovative bonding techniques between the diamond table and tungsten carbide substrate. This creates a stronger interface that resists delamination under extreme drilling conditions.
### 3. Optimized Thermal Management
High-performance cutters incorporate thermal barrier technologies that protect the diamond table from heat damage, maintaining cutting efficiency even at elevated temperatures.
### 4. Precision Geometry
The cutting edge geometry of top-tier PDC cutters is carefully engineered to maximize ROP (Rate of Penetration) while minimizing vibration and bit balling.
## Applications of Premium PDC Cutters
The best PDC cutters excel in various drilling environments:
– Hard and abrasive formations
– Directional and horizontal drilling
– High-temperature wells
– Deepwater drilling operations
– Unconventional resource development
## Choosing the Right PDC Cutter for Your Operation
Selecting the optimal PDC cutter requires careful consideration of:
– Formation characteristics
– Drilling parameters
– Bit design
– Expected drilling conditions
– Performance requirements
Consulting with experienced cutter manufacturers can help identify the best solution for your specific application.
## Maintenance and Handling Best Practices
To maximize the performance and lifespan of your PDC cutters:
– Store cutters properly to prevent damage
– Handle with care during installation
Keyword: best pdc cutter
– Monitor cutter wear during operations
– Follow manufacturer’s recommendations for reconditioning
– Keep accurate records of cutter performance
## The Future of PDC Cutter Technology
Ongoing advancements in PDC cutter technology include:
– Nano-structured diamond composites
– Improved thermal stability coatings
– Smart cutter designs with embedded sensors
– Enhanced wear-resistant materials
– Customized cutter solutions for specific applications
Investing in the best PDC cutter technology available today will position your drilling operations for success in an increasingly competitive industry. By focusing on quality, performance, and proper application, you can achieve superior drilling results and maximize your return on investment.