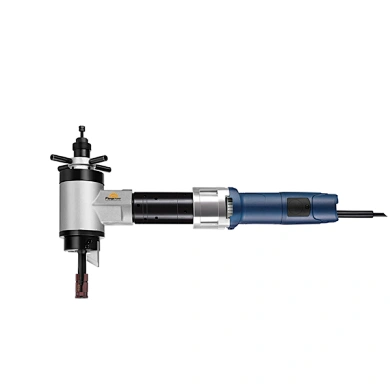
# Flange Facing Machine: Essential Tool for Precision Pipe Flange Preparation
## Introduction to Flange Facing Machines
Flange facing machines are specialized tools designed to prepare pipe flanges for optimal sealing and connection. These powerful machines play a critical role in industrial maintenance, pipeline construction, and repair operations where precise flange surface preparation is required.
## How Flange Facing Machines Work
A flange facing machine typically mounts directly onto the pipe flange and uses rotating cutting tools to machine the flange face to the required specifications. The machine’s design ensures concentricity and flatness while maintaining proper surface finish standards. Modern machines often feature adjustable feed rates, depth controls, and various cutter options to accommodate different flange materials and specifications.
Keyword: Flange facing machine
## Key Applications in Industry
Pipeline Construction and Maintenance
In pipeline work, flange facing machines ensure proper mating surfaces for gaskets, preventing leaks in critical fluid transport systems. They’re particularly valuable when joining sections of pipe or when repairing damaged flange surfaces.
Power Generation Facilities
Power plants rely on flange facing machines to maintain the integrity of high-pressure steam and cooling water systems where even minor leaks can cause significant efficiency losses or safety concerns.
Oil and Gas Industry
The oil and gas sector uses these machines extensively for both offshore and onshore applications, where they prepare flanges for connections that must withstand extreme pressures and corrosive environments.
## Advantages of Using a Flange Facing Machine
- Precision machining for optimal sealing surfaces
- On-site capability eliminates need for flange removal
- Time and cost savings compared to traditional methods
- Consistent results across multiple flange preparations
- Ability to work with various flange materials (carbon steel, stainless steel, etc.)
## Choosing the Right Machine for Your Needs
When selecting a flange facing machine, consider factors such as:
- Flange size range the machine can accommodate
- Power source requirements (electric, hydraulic, pneumatic)
- Portability and setup time
- Available cutter options and accessories
- Ease of operation and maintenance requirements
## Maintenance and Safety Considerations
Regular Maintenance
Proper maintenance of your flange facing machine includes regular lubrication, cutter inspection and replacement, and checking alignment components. Following the manufacturer’s maintenance schedule ensures consistent performance and extends machine life.
Safety Precautions
Always wear appropriate PPE when operating a flange facing machine, including safety glasses, hearing protection, and gloves. Secure the workpiece properly and ensure all guards are in place before starting the machine. Follow lockout/tagout procedures when performing maintenance.
## Conclusion
Flange facing machines represent an essential investment for any operation dealing with pipe flange connections. Their ability to deliver precise, on-site machining solutions makes them invaluable for ensuring leak-free, reliable connections in critical piping systems across numerous industries. By selecting the right machine and maintaining it properly, organizations can significantly improve their flange preparation processes while reducing downtime and repair costs.