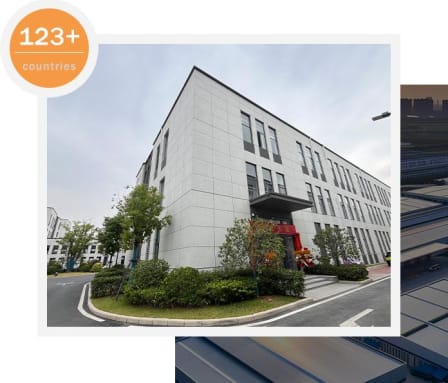
# PDC Cutter Manufacturing Facility: The Heart of Cutting-Edge Drilling Technology
PDC Cutter Manufacturing Facility: The Heart of Cutting-Edge Drilling Technology
In the world of modern drilling operations, PDC (Polycrystalline Diamond Compact) cutters have become indispensable components. These ultra-hard cutting elements are manufactured in specialized PDC cutter factories that combine advanced technology with precision engineering to produce tools capable of withstanding extreme drilling conditions.
The Manufacturing Process at a PDC Cutter Factory
A state-of-the-art PDC cutter manufacturing facility follows a meticulous production process:
- Material Selection: High-quality synthetic diamond powder and tungsten carbide substrates are carefully chosen
- High-Pressure, High-Temperature (HPHT) Synthesis: The diamond powder is subjected to extreme pressures and temperatures to form the polycrystalline diamond layer
- Precision Machining: The PDC blanks are ground and shaped to exact specifications
- Quality Control: Each cutter undergoes rigorous testing for hardness, wear resistance, and thermal stability
Key Features of a Modern PDC Cutter Factory
Leading PDC cutter manufacturing facilities incorporate several critical elements:
Advanced Equipment: HPHT presses capable of generating pressures exceeding 5 GPa and temperatures over 1400°C form the core of production.
Clean Room Environments: Critical assembly processes occur in controlled environments to prevent contamination.
Automated Quality Systems: Computerized inspection systems ensure consistent product quality across all batches.
The Importance of Research and Development
Top-tier PDC cutter factories maintain dedicated R&D departments focused on:
- Developing new diamond formulations for enhanced performance
- Improving cutter geometries for specific applications
- Testing new substrate materials for better impact resistance
- Optimizing manufacturing processes for increased efficiency
Applications of Factory-Produced PDC Cutters
The cutters manufactured in these specialized facilities find applications in:
Oil and Gas Drilling: PDC bits equipped with these cutters can drill faster and longer than conventional roller cone bits.
Mining Operations: Used in roadheaders and other mining equipment for hard rock excavation.
Geothermal Drilling: Withstand the high temperatures encountered in geothermal well drilling.
Construction: Employed in trenching and foundation drilling equipment.
Future Trends in PDC Cutter Manufacturing
The PDC cutter factory of tomorrow will likely incorporate:
Keyword: pdc cutter factory
- AI-driven process optimization
- Nanotechnology-enhanced diamond structures
- More sustainable manufacturing practices
- Advanced coating technologies for improved performance
As drilling challenges become more complex, the role of specialized PDC cutter manufacturing facilities becomes increasingly vital in developing the cutting tools that power modern exploration and extraction operations worldwide.