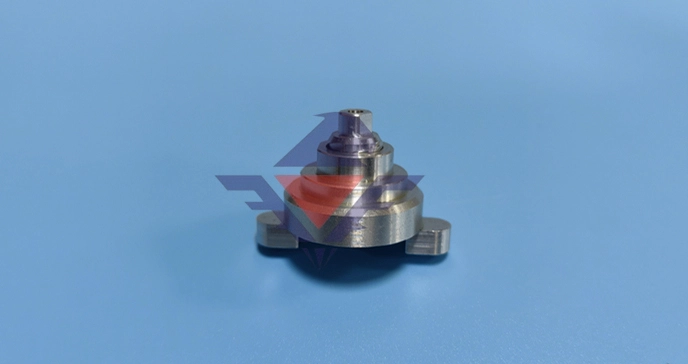
# Swiss Screw Machining: Precision and Efficiency in Small Part Manufacturing
## The Art of Swiss Screw Machining
Swiss screw machining, also known as Swiss turning or Swiss-style lathe machining, represents one of the most precise and efficient methods for manufacturing small, complex parts. Originating in Switzerland’s watchmaking industry during the 19th century, this technology has evolved to become indispensable in modern precision manufacturing.
## How Swiss Screw Machines Work
Unlike conventional lathes, Swiss screw machines feature a sliding headstock and guide bushing that provides exceptional support for the workpiece. This unique design allows for:
– Extreme precision in machining long, slender parts
– Simultaneous multiple operations
– Reduced vibration and improved surface finishes
Keyword: Swiss Screw Machining
– Tight tolerances (often within ±0.0002 inches)
## Key Advantages of Swiss Machining
### 1. Unmatched Precision
The guide bushing system in Swiss machines provides unparalleled stability, enabling manufacturers to achieve tolerances that would be impossible with conventional turning methods. This makes Swiss machining ideal for medical components, aerospace parts, and electronics where precision is paramount.
### 2. High Production Efficiency
Modern CNC Swiss screw machines can perform multiple operations in a single setup, including:
– Turning
– Drilling
– Milling
– Threading
– Grooving
This multi-tasking capability significantly reduces production time and eliminates the need for secondary operations.
### 3. Material Versatility
Swiss machines excel at working with a wide range of materials, from common metals like aluminum and stainless steel to exotic alloys and engineering plastics. The process is particularly effective for materials that are:
– Difficult to machine
– Prone to deflection
– Require intricate features
## Applications Across Industries
Swiss screw machining has found applications in numerous industries:
– Medical: Surgical instruments, implants, and diagnostic equipment components
– Aerospace: Precision fittings, hydraulic components, and fuel system parts
– Automotive: Fuel injection components, sensors, and transmission parts
– Electronics: Connectors, contacts, and miniature hardware
## Choosing the Right Swiss Machining Partner
When selecting a Swiss machining service provider, consider:
– Machine capabilities and technology level
– Quality control processes and certifications
– Experience with your specific industry requirements
– Capacity for prototyping versus production runs
The combination of Swiss machining’s precision, efficiency, and versatility continues to make it the gold standard for small part manufacturing across critical industries. As technology advances, these machines are becoming even more capable, pushing the boundaries of what’s possible in precision manufacturing.