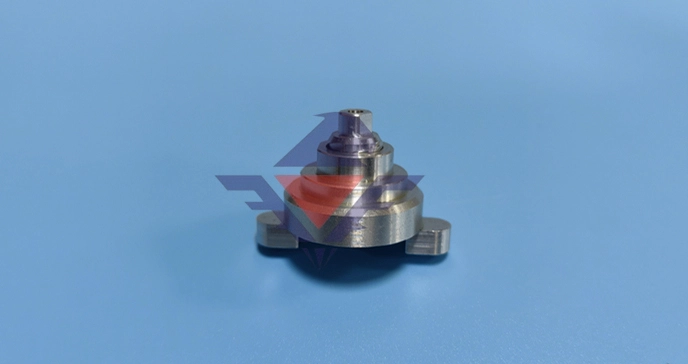
,文章长度约1000词左右
html
Swiss Screw Machining: Precision and Efficiency in Small Part Manufacturing
In the world of precision manufacturing, Swiss screw machining stands out as a highly specialized and efficient method for producing small, complex parts with exceptional accuracy. This advanced machining technique has revolutionized industries ranging from medical devices to aerospace by enabling the production of intricate components with tight tolerances.
The Origins and Evolution of Swiss Screw Machining
Originally developed in Switzerland during the late 19th century for watchmaking, Swiss screw machining (also known as Swiss turning or Swiss-type machining) was created to address the need for extremely precise small components. The watch industry required parts with diameters often less than 1mm, which conventional lathes couldn’t produce with sufficient accuracy.
Over time, the technology evolved from purely mechanical machines to today’s sophisticated CNC (Computer Numerical Control) Swiss screw machines. Modern iterations combine turning operations with milling, drilling, and other secondary processes, making them incredibly versatile manufacturing solutions.
How Swiss Screw Machining Works
The fundamental difference between Swiss screw machines and conventional lathes lies in the movement of the workpiece. In traditional turning, the workpiece rotates while the cutting tool moves linearly. Swiss machines reverse this relationship:
- The workpiece moves linearly through a guide bushing
- Cutting tools remain stationary relative to the bushing
- This configuration provides exceptional stability during machining
The guide bushing supports the material very close to the cutting area, minimizing deflection and vibration. This allows for much higher precision, especially when working with long, slender parts that would normally bend under cutting forces.
Key Advantages of Swiss Screw Machining
Keyword: Swiss Screw Machining
1. Unmatched Precision
Swiss machines routinely achieve tolerances within ±0.0002 inches (±0.005mm), making them ideal for critical components in medical implants, aerospace applications, and electronic connectors.
2. Superior Surface Finish
The inherent stability of the Swiss process produces excellent surface finishes, often eliminating the need for secondary finishing operations.
3. Reduced Material Waste
By machining parts complete in one operation, Swiss screw machining minimizes material waste compared to processes requiring multiple setups.
4. High Production Efficiency
Modern CNC Swiss machines can perform multiple operations simultaneously, dramatically reducing cycle times for complex parts.
Applications Across Industries
The unique capabilities of Swiss screw machining have made it indispensable in several high-tech industries:
Medical Device Manufacturing
From surgical instruments to implantable components, the medical field relies heavily on Swiss machining for parts requiring biocompatibility, extreme precision, and complex geometries.
Aerospace and Defense
Critical aircraft components, missile guidance systems, and satellite parts often utilize Swiss-machined components for their reliability and precision.
Electronics and Microtechnology
Connectors, sensor components, and miniature electronic housings benefit from the Swiss process’s ability to work with small diameters and tight tolerances.
Automotive Industry
Fuel injection components, transmission parts, and various sensors increasingly use Swiss-machined parts to meet modern performance requirements.
Material Capabilities
Swiss screw machines can work with an extensive range of materials, including:
- Stainless steels (303, 304, 316, etc.)
- Titanium and titanium alloys</