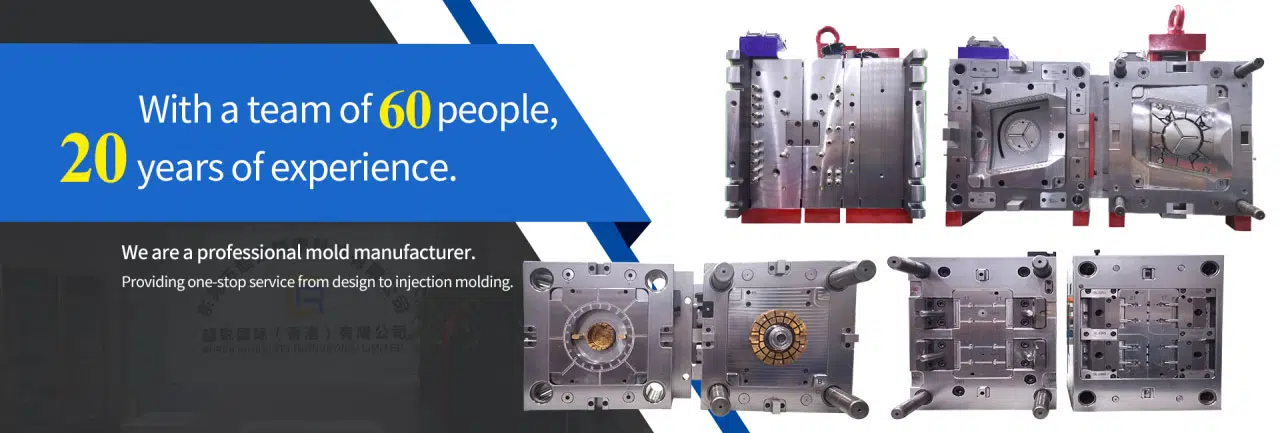
# Sand Casting Process Overview
## Introduction to Sand Casting
Sand casting is one of the oldest and most widely used metal casting processes. This versatile method has been employed for centuries to create metal parts of various sizes and complexities. The process involves pouring molten metal into a sand mold cavity, allowing it to solidify, and then breaking away the sand mold to reveal the finished casting.
## Key Components of Sand Casting
Keyword: Sand Casting
### 1. Pattern Making
The sand casting process begins with creating a pattern, which is a replica of the final product. Patterns can be made from wood, metal, plastic, or other materials. The pattern determines the shape and size of the casting cavity in the sand mold.
### 2. Mold Preparation
The mold consists of two parts: the cope (upper half) and the drag (lower half). These are created by packing specially formulated sand around the pattern in a molding box called a flask. The sand mixture typically contains:
– Silica sand (85-95%)
– Clay (5-10%)
– Water (2-5%)
### 3. Core Making (if needed)
For castings with internal cavities or complex geometries, sand cores are used. These are made separately from the main mold and are placed in the mold cavity before pouring the molten metal.
## The Sand Casting Process Steps
### Step 1: Pattern Placement
The pattern is placed in the drag (lower flask), and molding sand is packed around it. The sand is compacted to ensure proper mold strength.
### Step 2: Mold Assembly
After the drag is prepared, the cope (upper flask) is created similarly. The two halves are then assembled, with the pattern removed, leaving a cavity in the shape of the desired part.
### Step 3: Pouring
Molten metal is poured into the mold through a pouring cup and runner system. The metal fills the cavity and any cores that have been placed in the mold.
### Step 4: Cooling
The molten metal is allowed to cool and solidify within the mold. Cooling time depends on the metal used and the size of the casting.
### Step 5: Shakeout
Once solidified, the sand mold is broken away from the casting in a process called shakeout. The casting is then cleaned of any remaining sand and excess metal.
### Step 6: Finishing
The final step involves removing any rough edges (flash), machining critical surfaces, and performing any required heat treatments.
## Advantages of Sand Casting
– Cost-effective for small to medium production runs
– Can produce very large castings (up to several tons)
– Suitable for a wide range of metals and alloys
– Allows for complex geometries
– Relatively simple tooling requirements
## Common Applications
Sand casting is used across various industries to produce:
– Engine blocks and cylinder heads
– Pump housings
– Valves and fittings
– Large machine components
– Artistic sculptures and decorative pieces
## Conclusion
Sand casting remains a fundamental manufacturing process due to its versatility, cost-effectiveness, and ability to produce complex metal parts. While newer casting methods have been developed, sand casting continues to be widely used, especially for large or low-volume production runs where other methods would be prohibitively expensive.