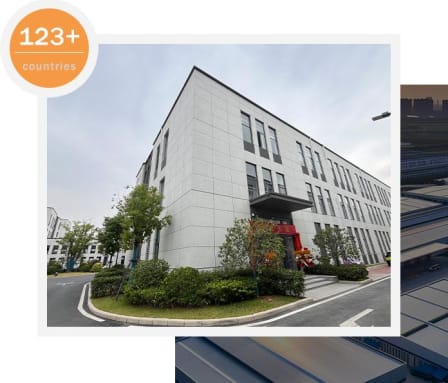
# PDC Bit Cutter Technology in Drilling Applications
## Introduction to PDC Bit Cutters
Polycrystalline Diamond Compact (PDC) bit cutters have revolutionized the drilling industry with their exceptional durability and cutting efficiency. These advanced cutting tools are widely used in oil, gas, and geothermal drilling operations, offering significant advantages over traditional roller cone bits.
Keyword: pdc bit cutter
## How PDC Cutters Work
The Structure of PDC Cutters
PDC cutters consist of two main components: a synthetic diamond table bonded to a tungsten carbide substrate. The diamond layer provides extreme hardness for cutting through rock formations, while the carbide substrate offers structural support and facilitates brazing to the drill bit body.
Cutting Mechanism
Unlike roller cone bits that crush rock through impact, PDC cutters shear rock formations with a continuous scraping action. This mechanism results in faster penetration rates and smoother operation, reducing vibration and improving borehole quality.
## Advantages of PDC Bit Technology
Superior Durability
PDC cutters maintain their sharp cutting edges much longer than conventional bits, significantly extending bit life and reducing the frequency of bit changes during drilling operations.
Increased ROP
The continuous shearing action of PDC bits typically achieves 2-4 times higher Rate of Penetration (ROP) compared to roller cone bits in suitable formations.
Reduced Downhole Vibrations
The smooth cutting action minimizes harmful vibrations that can damage downhole equipment and reduce drilling efficiency.
## Applications in Various Drilling Environments
Oil and Gas Drilling
PDC bits dominate modern oilfield drilling, particularly in soft to medium-hard formations where they offer the best combination of speed and durability.
Geothermal Drilling
The heat-resistant properties of PDC cutters make them ideal for high-temperature geothermal applications where conventional bits would fail prematurely.
Mining and Construction
PDC technology has found applications in mineral exploration and construction drilling where hard rock penetration is required.
## Recent Technological Advancements
Thermally Stable PDC (TSP) Cutters
New formulations of PDC cutters with enhanced thermal stability allow operation in harder formations and higher temperature environments.
Customized Cutter Geometries
Manufacturers now offer specialized cutter shapes and orientations optimized for specific formation types and drilling conditions.
Advanced Bonding Techniques
Improved bonding methods between the diamond table and carbide substrate have significantly increased cutter reliability and impact resistance.
## Future Trends in PDC Technology
The drilling industry continues to push the boundaries of PDC cutter performance. Research focuses on developing even more wear-resistant diamond composites, smarter bit designs with embedded sensors, and hybrid technologies that combine the benefits of PDC and other cutting mechanisms.
As drilling operations move into more challenging environments, PDC bit cutter technology will remain at the forefront of innovation, helping operators achieve greater efficiency and lower costs in their drilling programs.