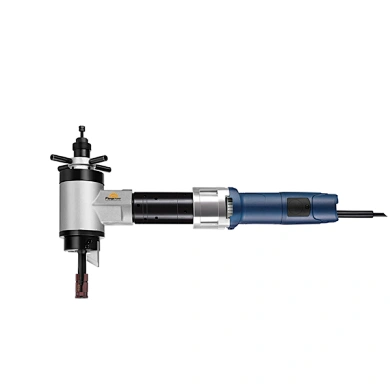
# Flange Facing Machine: Essential Tool for Precision Flange Resurfacing
## What is a Flange Facing Machine?
A flange facing machine is a specialized piece of equipment designed for on-site machining of flange surfaces. These portable machines are engineered to restore damaged or corroded flange faces to their original specifications without requiring removal of the flange from the pipeline or vessel.
## Key Features of Modern Flange Facing Machines
Modern flange facing machines incorporate several advanced features that make them indispensable for industrial maintenance:
- Portable design for field use
- Precision cutting capabilities
- Adjustable cutting speeds
- Multiple tooling options
- Digital measurement systems
## Applications in Various Industries
Oil and Gas Sector
In the oil and gas industry, flange facing machines are critical for maintaining pipeline integrity. They’re used to repair flange surfaces damaged by corrosion, erosion, or improper gasket seating.
Power Generation
Power plants rely on these machines to maintain steam and water system flanges, ensuring leak-free connections in high-pressure environments.
Chemical Processing
The chemical industry uses flange facers to maintain critical sealing surfaces that prevent hazardous material leaks.
## Benefits of Using a Flange Facing Machine
The advantages of using a professional flange facing machine include:
- Cost savings by avoiding flange replacement
- Reduced downtime during maintenance
- Improved safety through proper sealing surfaces
- Precision results matching OEM specifications
- Versatility for various flange sizes and materials
## Choosing the Right Flange Facing Machine
Keyword: Flange facing machine
When selecting a flange facing machine, consider these factors:
- The range of flange sizes you need to service
- Material types you’ll be machining (steel, stainless, etc.)
- Available power sources at your work sites
- Required precision levels for your applications
- Portability and setup time requirements
## Maintenance Tips for Optimal Performance
Regular Cleaning
After each use, thoroughly clean the machine to remove metal chips and debris that could affect performance.
Tool Inspection
Regularly inspect cutting tools for wear and replace them as needed to maintain cutting quality.
Lubrication Schedule
Follow the manufacturer’s recommended lubrication schedule for all moving parts.
## Conclusion
Flange facing machines have become essential tools for industrial maintenance teams. Their ability to precisely resurface flanges on-site saves time and money while ensuring proper sealing integrity. By selecting the right machine and maintaining it properly, facilities can significantly extend the service life of their flange connections.